- Home
-
All Categories
- Automotive
- Camera & Photo Products
- Arts, Crafts & Sewing
- Patio, Lawn & Garden
- Toys & Games
- Kitchen & Dining
- Industrial & Scientific
- Home & Kitchen
- Clothing, Shoes & Jewelry
- Tools & Home Improvement
- Electronics
- Sports & Outdoors
- Office Products
- Musical Instruments
- Video Games
- Computers & Accessories
- Pet Supplies
- Sports Collectibles
- Appliances
- Grocery & Gourmet Food
- Health & Household
- Baby
- Cell Phones & Accessories
- Beauty & Personal Care
- Software
- Payment
- About Us
- FAQ
- Privacy Notice
- Shipping & Returns
- Contact Us
Your cart is empty.
Your cart is empty.Product Description
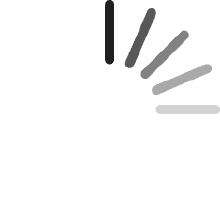
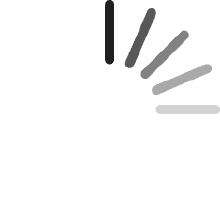
The world's largest selection of powder coating colors!
Uniform Coverage | Ensures, smooth surface without runs or drips, as the powder coating powder melts and flows evenly during curing. |
Variety of Finishes | Available in a wide range of colors, textures, gloss levels, including matte, satin, and high gloss. |
Versatility | Powder coating can be applied to metal, steel, aluminum, and other conductive surfaces. |
Fast Drying and Curing | Reduces processing time, as powder coating paint cures quickly under heat. |
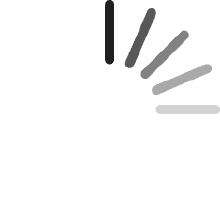
PLEASE REFER TO EACH POWDER’S TECHNICAL DATASHEET FOR SPECIFIC PRODUCT INFORMATION
PREP
- Remove all coatings, oils, and contaminants from the substrate with either a chemical stripper or a degreasing agent (Acetone, Brake Parts Cleaner, or Simple Green); these are some examples of chemical strippers and degreasers that work well depending on the condition of the substrate.
- Plug/mask off any areas that you do not want to be coated. Improper masking on certain mechanical parts or mating surfaces may cause tolerance or functionality issues.
PRE-TREATMENT
- A sand-blasted profile is highly recommended for the substrate to remove any rust, scale, or other coatings. This is also a crucial step to ensure maximum coating adhesion.
- Fixture part(s) to allow for the best view and application access; this can be done by using support hooks and support wires.
- Blow off the substrate with a high-pressure air nozzle to remove any sandblasting media/dust left on the surface. Work in a well-ventilated area and always wear proper Personal Protective Equipment (PPE), e.g., safety goggles and respirator.
- We recommend but do not require, that parts are placed in an oven at 450ºF (232°C) for approximately 30 minutes. This will aid in discharging part(s) that have developed any static charge and evaporate any surface moisture or solvents from degreasing. If contaminates are drawn to the surface during this phase, the affected areas will need to be addressed. Applying Prismatic Powder Anti-Gas Primer can assist with parts more prone to outgassing (ESS-11152).
APPLICATION
- Confirm all ground connections are properly made before the application begins. As mentioned above, a true earth-ground connection is always considered as best practice.
- Adjust your gun’s settings to provide an adequate powder cloud that is not projecting too much powder but also not too little. You will be looking to verify that the spray gun does not surge while the trigger is pulled. If it does, additional gun/hopper adjustments will need to be made.
- In some instances, a gun system will come with multiple nozzle options (conical, fan, & castle). These nozzles will alter the powder path in different ways and can be advantageous for specific coating scenarios.
- Once you believe adequate coverage has been achieved, we recommend utilizing a light source to check over your work. Add additional coating if needed.
CURING
- If additional layers of powder are expected to be applied, it’s imperative to flash/partially cure each layer beforehand. A flash cure will be based on a visual inspection of the coating just reaching the flow-out phase.
- Visually confirm the part(s) have completely flashed (reached the liquid-looking state) and wait an additional 2 – 3 minutes before removing the parts from the oven. Metallic coatings will require 3 – 5 additional minutes following the flash phase. This additional time helps to set the metallics in place.
- Once the part(s) are cooled to room temperature, check mil thickness to see if additional coats are required. For most powder applications, we recommend 2 – 3 mils (0.002 – 0.003) per coat. • When the part(s) have been completely coated, place them in the oven for a final cure cycle. This means you will need to confirm that the thickest portion of the substrate reaches cure temperature before starting the cure timer.
- Cure schedules can be found on powder bag label.
Always follow the cure schedule for the last powder applied to effectively cure any previous layers.
$17.69 $17.69
$ 8 .99 $8.99
$15.80 $15.80
$ 7 .99 $7.99
$24.18 $24.18
$ 10 .99 $10.99
$29.00 $29.00
$ 12 .99 $12.99
$39.33 $39.33
$ 19 .99 $19.99
$14.04 $14.04
$ 6 .99 $6.99
$212.87 $212.87
$ 90 .99 $90.99