- Home
-
All Categories
- Automotive
- Camera & Photo Products
- Arts, Crafts & Sewing
- Patio, Lawn & Garden
- Toys & Games
- Kitchen & Dining
- Industrial & Scientific
- Home & Kitchen
- Clothing, Shoes & Jewelry
- Tools & Home Improvement
- Electronics
- Sports & Outdoors
- Office Products
- Musical Instruments
- Video Games
- Computers & Accessories
- Pet Supplies
- Sports Collectibles
- Appliances
- Grocery & Gourmet Food
- Health & Household
- Baby
- Cell Phones & Accessories
- Beauty & Personal Care
- Software
- Payment
- About Us
- FAQ
- Privacy Notice
- Shipping & Returns
- Contact Us
Your cart is empty.
Your cart is empty.- Home /
- Industrial & Scientific
- Fasteners
- Additive Manufacturing Products
- Lab & Scientific Products
- Hydraulics, Pneumatics & Plumbing
- Industrial Hardware
- Food Service Equipment & Supplies
- Raw Materials
- Industrial Electrical
- Adhesives, Sealants & Lubricants
- Professional Medical Supplies
- Janitorial & Sanitation Supplies
- Material Handling Products
- Professional Dental Supplies
- Power Transmission Products
- Packaging & Shipping Supplies
- Test, Measure & Inspect
- Occupational Health & Safety Products
- Science Education
- Retail Store Fixtures & Equipment
- Cutting Tools
- Filtration
- Abrasive & Finishing Products
- Robotics
- Commercial Door Products
- Digital Signage
- Power & Hand Tools
/
- Additive Manufacturing Products /
- 3d Printer Parts & Accessories /
- 3d Printer Motors
Product Description
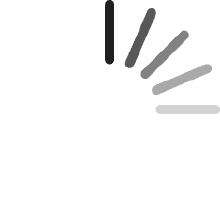
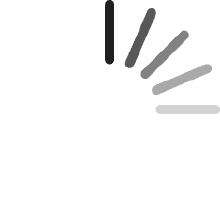
DM542 STEPPER MOTOR DRIVER
Advantages:
- The driver integrates over-voltage, over-current, and wrong-phase protection fuctions.
- Strong-anti-interference ability, can achieve high-precision positioning in the harsh environment of the power grid.
- High reliability: power devices have enough margins, and they have strictly tested before leaving the factory.
Applications
Suitable for various automation equipment and instruments in the field of motion control, such as:
3D printers, engraving equipment, medical equipment, measuring equipment, electronic processing equipment, textile and clothing equipment, etc.
Use environment and parameters
- Cooling method: natural cooling or forced air cooling
- Occasion: Avoid dust, oil, corrosive gas, high humidity and strong vibration
- Place, no flammable gas and conductive dust
- Temperature: 0℃—50℃
- Humidity: 40-90%RH
- Vibration: 10-55Hz/0.15mm
- Storage temperature: -20℃—65℃
Features:
- Input signal optical isolation
- Bipolar constant current chopping method
- DC power supply 20-50VDC (recommended 24-48VDC)
- Maximum driver current 4.2A
- Adjustable output current DIP switch
- Low speed and zero vibration, minimal noise
- High subdivision: 2, 4, 8, 16, 64, 128, 5, 10, 20, 25, 40, 50, 100, 125
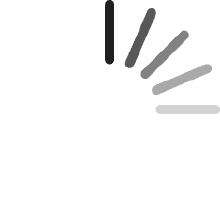
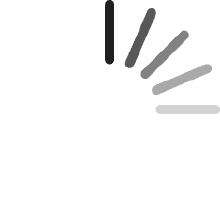
Power /Motor interface
- V: DC power supply positive pole, range +20V—+50V
- GND: DC power supply negative
- A+ A-: Motor phase A winding
- B+ B-: Motor B-phase winding
3. ENA+, ENA-, enable control signal
This input signal is used to enable or disable the driver output. When ENA is connected to low level (or the internal optocoupler is on), the driver will cut off the current of each phase of the motor so that the motor is in a free state and does not respond to step pulses. When this function is not needed, the enable signal terminal can be left floating. 5-24VDC level compatible.
INTERFACE DEFINITION
Control signal interface
1. PUL+, PUL-, pulse input signal
The effective edge of the pulse is adjustable, and the rising edge of the pulse is effective by default; in order to reliably respond to the pulse signal, the pulse width should be greater than 1.2us. 5-24VDC level compatible.
2. DIR+, DIR-, direction input signal
For high/low level signals, to ensure reliable commutation of the motor, the direction signal should be established at least 5us before the pulse signal. The initial running direction of the motor is related to the wiring of the motor windings, swapping any phase winding (such as A+, A- swapping) can change the initial running direction of the motor. 5-24VDC level compatible
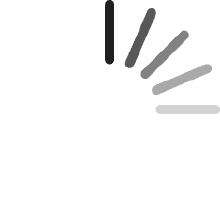
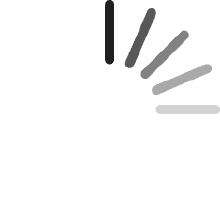
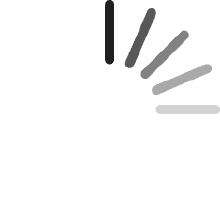
$19.57 $19.57
$ 9 .99 $9.99
$23.00 $23.00
$ 9 .99 $9.99
$283.66 $283.66
$ 99 .00 $99.00