- Home
-
All Categories
- Automotive
- Camera & Photo Products
- Arts, Crafts & Sewing
- Patio, Lawn & Garden
- Toys & Games
- Kitchen & Dining
- Industrial & Scientific
- Home & Kitchen
- Clothing, Shoes & Jewelry
- Tools & Home Improvement
- Electronics
- Sports & Outdoors
- Office Products
- Musical Instruments
- Video Games
- Computers & Accessories
- Pet Supplies
- Sports Collectibles
- Appliances
- Grocery & Gourmet Food
- Health & Household
- Baby
- Cell Phones & Accessories
- Beauty & Personal Care
- Software
- Payment
- About Us
- FAQ
- Privacy Notice
- Shipping & Returns
- Contact Us
Your cart is empty.
Your cart is empty.- Home /
- Tools & Home Improvement /
- Electrical
- Breakers, Load Centers & Fuses
- Plugs
- Recessed Lighting
- Travel Adapters
- Outlets & Accessories
- Ballasts
- Testers
- Electrical Boxes, Conduits & Fittings
- Tools & Hardware
- Switches & Dimmers
- Electric Motors
- Door Chimes & Bells
- Cords, Adapters & Multi-outlets
- Timers
- Light Sockets
- Electrical Wire
- Electrical Connectors
- Extension Cords
- Home Automation Devices
- Wall Plates & Accessories
/
- Electric Motors /
- Mounts & Accessories /
- Controls
Product Description
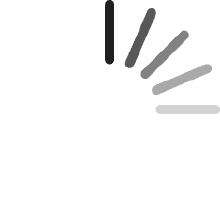
Stepper motor Driver Specification
- Support EtherNET
- 7ports input interface for ordinary digital data
- 3 ports output interface for ordinary digital data
- 1 port 0-10V spindle speed analog output interface(can change to PWM output)
- can support 4 axis stepper systems,300KHz pulse output for every axis
- ARM motion control chip
- Compatible with MPG input, support stardand MPG & the digital display MPG of our company
- Each axis driver supports 256 subdivisions at most
- Each axis driver supports 6A current
- The static current, running current and subdivision of the driver can be adjusted. The adjustment position is on the plug-in page of mach3.
Package Include:
- 1 x 4 Axis LAN5160T4 Stepper Motor Driver
- 1 x 6 Axis MPG Pendant Handwheel with Emergency Stop
- 1 x Ethernet Network Interface Card
- 1 x Cable
6 Axis Electromic Handwheel
- Resolution ( CPR ) : 25,100
- Operating Voltage: 5-12V
- Switch: X1,X10,X100
- Axis Switch: OFF, X, Y, Z, 4, 5, 6
- Response Frequency: 0-10KHz
4 Axis Stepper Motor Driver
- LAN5160T4 is the 4 axis motion controller & driver,we spend 4 years to design. This controller’s control cycle is 2ms. The maximum pulse frequency of each axis is 300KHz. The highest division is 256.The highest current is 6A.
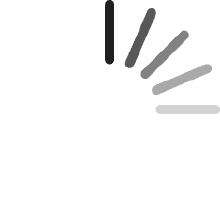
LAN5160T4 Connection Define and Method
1. Indicator light: The power indicator and the link indicator.
- The two lamps are arranged vertically, with the red one at the bottom, the blue one at the top, and the red one as the power indicator. When the power is turned on, it will light up; The blue indicator is the link indicator. When the mach3 is turned on and the mach3 software and the board are connected normally, the blue indicator is on. When the mach3 software is turned off, the blue indicator is off.
2. MPG port: Three row DB15 interface. The interface definition is printed on the cover.
3. Ethernet port:
- Through which the controller can be connected to the computer. The controller supports both router mode and network cable direct connection mode.
4. Input interface: General input interface, which is a DB9 interface. The specific definition is printed on the shell.
5. ESTOP input port:
- The interface form is an XH2P terminal. The specific definition is marked on the shell, which is defined as COM -/IN1 respectively. When using, connect the two terminals of the emergency stop switch to COM - and IN respectively.
6. Spindle Port: COM - to connect the inverter ACM/DCM, OUT1 to connect the inverter FWD, and VSO to connect the inverter AVI.
7. Relay control port:
- The relay output interface is also in the form of XH3P interface, which is defined as COM -/OUT2/OUT3. It can be connected with two relays, which can output the ground opening signal and the maximum absorption current is 50mA. If a relay with a control current of more than 50mA is used, an external amplifier circuit is required.
8. Power input port:
- The power supply voltage range is 12V-36V, and 24V is strongly recommended. It is recommended that the power supply should not be less than 200W (determined according to the actual control stepping motor power).
9. stepper motor port:
- The minimum support is 0.5A current 2-phase stepping motor, and the maximum support is 6A current 2-phase stepper motor.
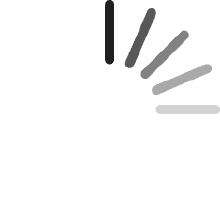
Substantival Explanation
When operate the LAN5160T4,where will be a lot of English abbreviation,now we list all of them for your kindly references:
- FRO: Feedingadjust:During the operating process,the F value already set,and need to adjust the current feeding speed, then we can adjust FRO value to realize it.
- SRO: Spindle speed adjust: During the operating process, the S value already set, and need to adjust the current spindle speed, then we can adjust SRO value to realize it :
Current Speed S#=setting S*SRO.
- SRJ: speed adjust manually. During the operating process,as the manual speed already set,and we need to adjust the current speed,and impossible to fix the value during it is working,then we can revise the SRJ value to realize it.
Current manual speed FS#=Setting manual speed*SRJ
- F: Feedingspeed,the unit is mm/min.For example F=200,means every minute feeding 2000mm.
- S: Spindle Speed. Unit is rad/min.For example S=20000,means 20000 revolution/Minute.
- X: X axis Coordinate
- Y: Y axis Coordinate
- Z: Z axis Coordinate
- A: A axis Coordinate
Definition of MPG Interface
- TX: Serial port sending pin
- 5V: 5V power pin
- A+/B+: encoder A+/encoder B+
- X: X axis select pin
- RX: Serial port receiving pin
- 0V: COM ground
- A-/B-: encoder A-/encoder B-
- Y/Z/A: Y/Z/A axis select pin
- 100: X100 rate select pin
- 10: X10 rate select pin
Definition of Universal Input Interface
- COM+: Common+,External supply 24V
- IN2: INPUT PIN2
- IN4: INPUT PIN4
- IN6: INPUT PIN6
- COM-: Common terminal-
- COM-: Common terminal-
- IN3: INPUT PIN3
- IN5: INPUT PIN5
- IN7: INPUT PIN7
LAN5160T4 Description
- LAN5160T4 support Mach3 software and serial port MPG, through ethernet to communcate with computer.
- LAN5160T4 motion controller adopts the ARM design framework. The ARM design includes communication, codeanalytic, underlying algorithm and pulse gerneration. Rationaldesign, reliablecontrol, convenient operation.
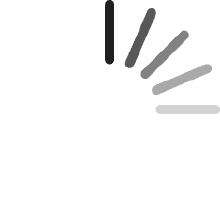
The all-plastic housing has high insulation strength, which can realize 4 axis (or 6 axis) selection switching. Metal gear, accutate scale, high precision and good texture.
With X1/X2/X100 triple gear ratio, optional emergency stop switch for control switch.
Lengthened CNC wire has good flexibility and elasticity, good colde resistance, flame resistance, andabrasion resistancce.
$10.44 $10.44
$ 5 .99 $5.99
$26.99 $26.99
$ 13 .99 $13.99
$239.99 $239.99
$ 99 .00 $99.00
$13.21 $13.21
$ 5 .99 $5.99
$29.09 $29.09
$ 13 .99 $13.99
$208.99 $208.99
$ 99 .00 $99.00
$72.99 $72.99
$ 31 .99 $31.99